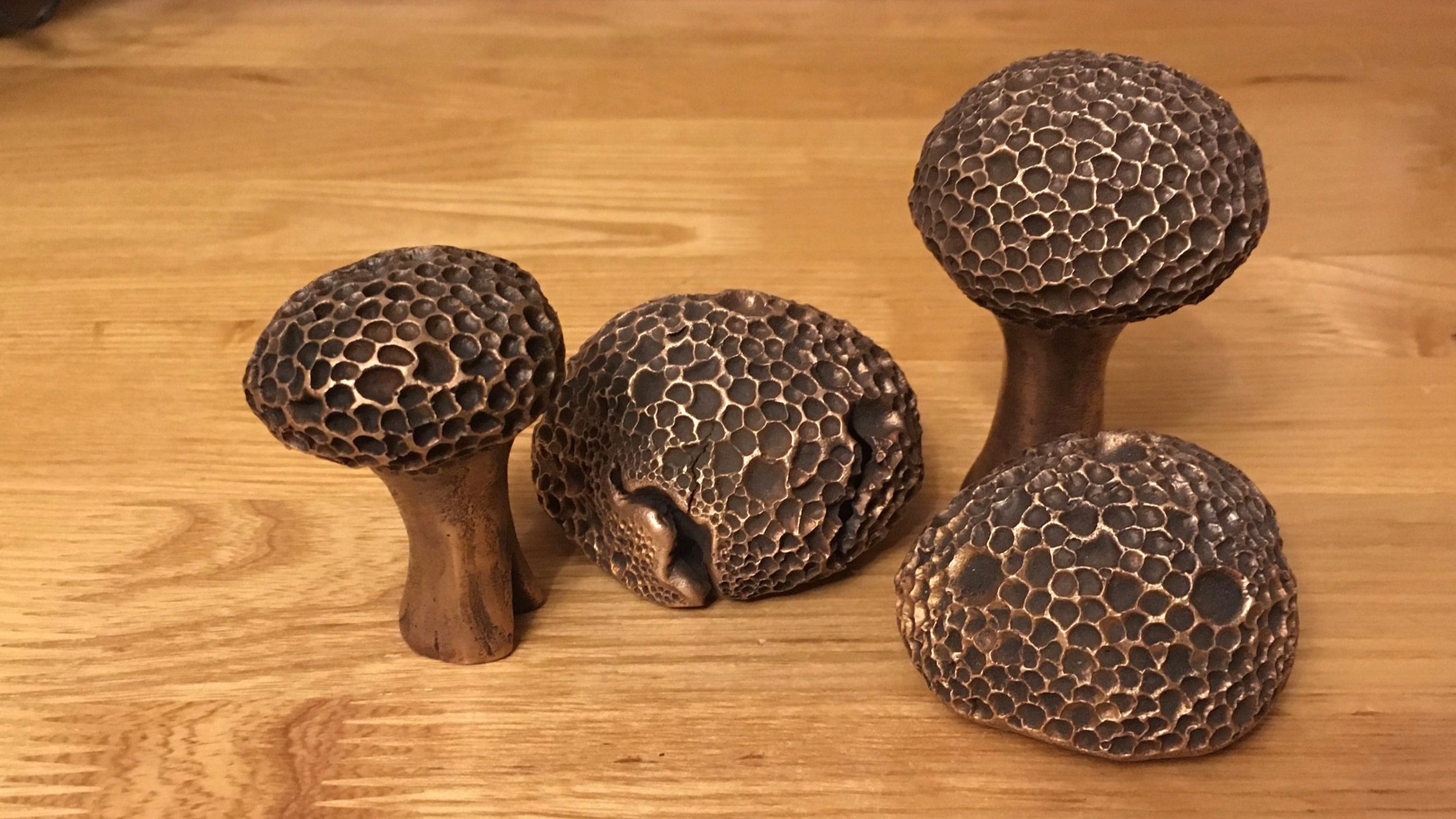
A new take on bronze sculpture
See the gallery for finished and in-progress pieces
The process of making bronze sculpture has changed little since the time of Rodin.
And even he would have been lost without expert craftsmen—themselves veritable artists—to translate his ideas from plaster, marble, or clay into metal. Lost-wax casting, the standard method for producing bronze sculpture, is simply too complex for an individual to undertake at scale; you need the support of a foundry. Because of the labor, time, and equipment required, commissioning a foundry to cast sculptures is financially daunting.
My method is a bit different.
Not only does it require fewer steps and less technical expertise, it’s also far quicker: once you finish sculpting a piece, you’re only a few days from having it reproduced in bronze. So how does it work?
Step 1: Sculpt an original
This is where you put on your beret and unleash your artistic passion (or smoosh clay into a fun shape). I usually use oil clay that remains pliable, but most sculpting media would work.
Step 2: Make a mold
Use the original to make a reusable mold. In this case, I used silicone rubber (blue in the image).
Step 3: Make a hollow cast
I mix a slurry of fine bronze powder and an organic binder to make a hollow cast of the original. In the image, I’m ready to combine the bronze with an acrylic binder to “slush-cast” a hollow piece.
Step 4: Fire!
Firing the casts in a kiln burns off the organic binder (around 300 °C) and causes the fine bronze particles to fuse in a process known as sintering (around 800 °C). By comparison, liquid bronze is typically around 1200 °C when poured.
Step 5: Finish
This step alone can take days in the lost wax process. Bronzes need to be liberated from a single-use ceramic mold and “chased” to reveal the final piece. However, my pieces need minimal cleanup: after sintering, they retain an oxide coating that can be brushed off or dissolved. The bright pieces in the forest at right are freshly fired and cleaned in preparation for the patina that will give them the richer tones of classic bronzes.
Step 6: Enjoy, mostly
The pieces shrink slightly as the bronze particles fuse, and this combined with the burnout of the organic binder can cause cracks or worse. Fortunately, the failure rate is low (I estimate around 5%) and some failures—like this one, which became a business card holder—have unintended charm.